安庆石化6亿元撑起一片蓝天
时间:2015-04-29 00:00来源: 作者:老网站
安庆石化6亿元撑起一片蓝天
作者:吴明 张晓梅 张骅
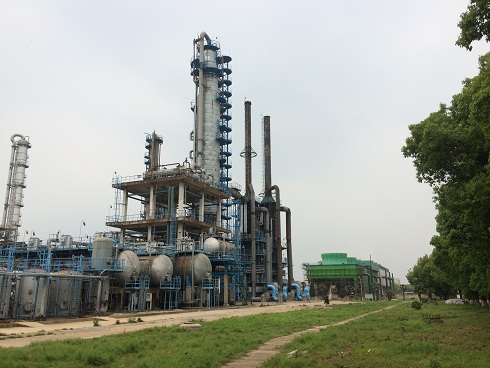
安庆石化厂区一角
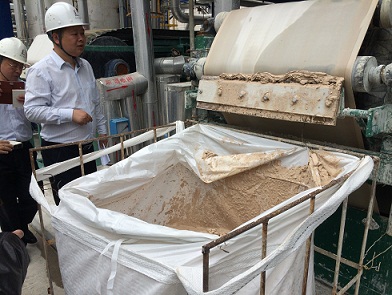
经过最新除尘化气装置处理留下的石膏等残留物
日前,安庆石化党委副书记王华清在向中央媒体采访团介绍环境治理情况时表示,近年来,安庆石化在加快企业有效发展的同时,同步加大环境污染治理的力度。从2013年底至今,安庆石化用于“碧水蓝天”工程的投入将超过6亿元,这几乎占到了公司日常年份全年投资额的80%以上。尽管与其他投资项目相比,“碧水蓝天”工程带来的更多是环境改善的社会效益,但安庆石化人认为,为了保护环境,这样的投资“值”!
正是由于全体参战人员高度的责任感和使命感,相关项目才能按照节点如期投入运行。从目前装置运行效果看,安庆石化“碧水蓝天”工程带来的治理成效明显。
其中,3、6号炉完成脱硫改造后,烟气中二氧化硫含量降到了100mg/Nm³以下,而此前二氧化硫的含量在800~1000mg/Nm³,脱硫率远远超过了90%的设计值。预计,仅此一项年减排二氧化硫4000吨以上(相当于再造8万亩树林)。4台锅炉脱硝项目投用后,脱硝率达到85%以上,锅炉出口烟气中氮氧化物排放浓度降到80mg/m³左右,预计年减排氮氧化物7000吨(相当于30万辆机动车全年的排放量)。
140万吨/年催化裂化装置改造后,烟气中二氧化硫含量从470mg/Nm³降至100mg/Nm³以下,颗粒物浓度从150mg/Nm³降到50mg/Nm³以下,预计年减排二氧化硫570吨,减排粉尘100吨(按年运行时间8000小时计算)。70万吨/年催化裂解装置改造后,烟气中的二氧化硫含量从320mg/Nm³降至50mg/Nm³以下,颗粒物浓度从200mg/Nm³降至50mg/Nm³以下,每年可减排二氧化硫40多吨,减排粉尘450吨(按年运行时间8000小时计算)。
据安庆石化安全环保部副部长肖春宝介绍,安庆石化“碧水蓝天”工程是中国石化“碧水蓝天”环保计划(2013年7月30日,在联合国全球契约中国网络主办的“生态文明•美丽家园”关注气候中国峰会上,中国石化宣布实施“碧水蓝天”环保计划。该计划提出,在2013年至2015年三年间,投入近230亿元,实施803个环保综合整治项目。这是中国石化发展史上规模最大的环保治理行动。)的一部分。实施该工程主要目的是为了进一步降低生产装置排放的硫化物、氮氧化物和粉尘含量,最大程度减少对大气的污染,深层“呵护”碧水蓝天。
安庆石化实施的“碧水蓝天”工程共有五项改造内容,其中,热电锅炉装置改造包含2个项目,分别是3、6号锅炉烟气脱硫改造(4、5号炉的脱硫改造已于2010年实施)和3、4、5、6号锅炉的烟气脱硝改造工程;炼油老区装置改造也包含2个项目,分别是140万吨/年催化裂化装置烟气脱硫脱硝项目和70万吨/年催化裂解装置烟气治理项目。上述4个项目,累计投资近5亿元,目前已经全面建成投用。另外,炼油新区的200万吨/年催化裂化装置烟气脱硫脱硝项目,计划投资1.4亿元,目前已经进入工程设计阶段,计划今年年内实施。
由于近年来,国家对环保的要求越来越严格,为了做到全面稳定达标排放,安庆石化在“碧水蓝天”工程中,采取了“紧盯标准达标”和“超前谋划实施”相结合的方式。同时,为了获得最大的环保效果,安庆石化不仅采用了最先进的环保技术,而且在环保理念上更加先进。
如:这次实施的3、6号锅炉烟气脱硫改造工程。实际上早在2006年安庆石化就对3、6号锅炉烟气应用过“干法”脱硫技术,满足了当时的国家排放标准要求。这次他们又投入近亿元再次进行改造,采用了石灰石—石膏“湿”法脱硫技术。这种从“干”到“湿”的技术变化,带来的不仅是装置脱硫效率的大幅度提升,而且很好地应用了循环经济发展的理念,将原本对大气造成污染的外排烟气中的二氧化硫直接转化成了具有一定价值的石膏产品。此项改造于2013年12月开工建设,2014年7月投入运行。
热电4台锅炉的烟气脱硝改造,采用了 “低氮燃烧器+选择性催化还原”技术,将装置产生的氮氧化物还原成无害的氮气排放。项目总投资近2亿元。由于热电锅炉大部分改造都是在正常生产时实施,所以安庆石化采取统筹协调、错开改造的方式逐个进行。6号炉脱硝于2014年7月投入运行,3号炉同年10月投运,4号炉同年12月投运,5号炉于2015年2月投运。
140万吨/年催化裂化装置烟气脱硫脱硝项目也采用了国外先进的环保技术。其中,脱硫采用美国杜邦贝尔格公司的先进技术,既能除去烟气中的二氧化硫,又能除去其中的催化剂颗粒;脱硝采用丹麦托普索公司的选择性催化还原技术,将烟气中的氮氧化物还原成无害的氮气排放。项目总投资1.42亿元,2015年2月投运。
70万吨/年催化裂解装置烟气治理项目,则是安庆石化在环保上追求“没有最好、只有更好”的一个典型范例。因为按照现行标准,即使装置不改造,也完全可以实现达标排放。但为了未雨绸缪,安庆石化选择了自我加压,投资近4000万元对其进行烟气治理。该项目含脱硫和电除尘两个单元,能深度脱除二氧化硫和烟尘。前者利用数个化学反应将烟气中的二氧化硫转化成硫磺回收装置的原料;后者采用比利时哈蒙公司的电除尘技术,利用电场收集烟气中的烟尘颗粒。脱硫单元2014年10月投运,电除尘单元2015年1月投运。
由于上述大部分改造都需要在装置正常生产的环境下进行,这既增大了施工的难度,又增加了生产的压力。尤其是进行热电锅炉改造时,由于热电锅炉担负着向全厂装置供电供热的重任,锅炉改造期间,在运锅炉没有备用炉,一旦出现问题,就会影响到全厂的生产。为了保证生产和施工两不误,安庆石化一方面超常规工作,一方面与参建单位密切配合。在整个工程建设中,参战单位和部门放弃休息日,全程参与质量把关和安全监护,尤其对每台设备的试运验收进行严格把关,及时解决问题、消除隐患。
在顺利完成热电3号、6号炉烟气脱硫和6号炉脱硝改造后,安庆石化以此为样板,总结经验,将其运用到余下的项目建设中。他们严抓“安全、质量、进度和生产准备”四个环节,在具体工作中做到提前介入、充分准备、紧密衔接、有效推进,使其他改造项目在边生产的同时得以顺利推进和完成。在此期间,面对生产区域施工,环境复杂、场地狭小、质量要求高的客观条件,安庆石化采用“5+2”、“白加黑”的工作模式,合理组织和安排施工,并根据实际情况不断优化施工方案,同时对施工质量进行全过程把关,确保施工质量,防止返工影响工期。尤其是对特殊材料焊接质量把关,坚持每周掌握焊接动态,一旦周焊接质量合格率降低,就立即分析原因,及时整改,确保质量。 - 上一篇:凯翼C3R配置曝光 打造A0越级智惠车
- 下一篇:奇瑞MPV定名艾瑞泽M7
相关文章
- 05-08目标20万辆 奇瑞集团单月出口刷新20年纪录
- 09-25安庆石化炼化新区投产一周年系列报道之二:转
- 12-29芜湖“Q乐节”在欢乐声中迎来奇瑞QQ冰淇淋起飞
- 05-25安徽省推出加快建设金融和资本创新体系实施意
- 04-08上海车展JAC品牌日全面展现“品牌向上”魅力
- 08-07奇瑞J.D.POWER销售服务满意度大幅提升 转型成效显
- 06-24阿根廷国际车展开幕奇瑞携主力车型盛装亮相
- 11-05合肥高新区获批国家知识产权服务业集聚发展试
- 04-21半自动驾驶“黑科技”助瑞风S7技术跃进
- 09-2078家央企携164个项目2290亿元助安徽发展